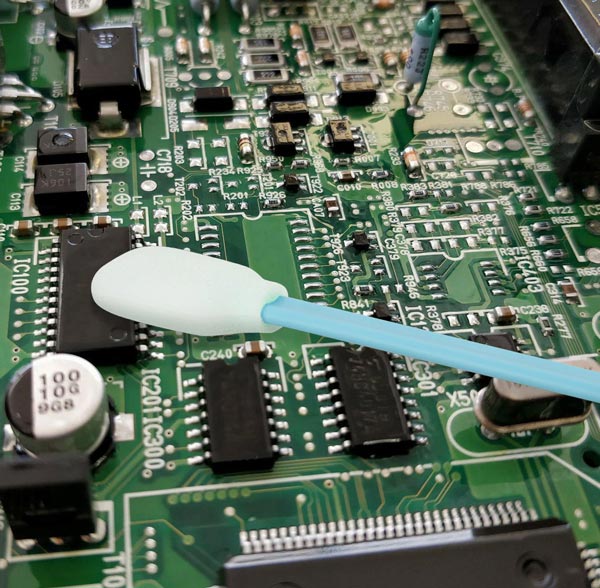
Dans la fabrication électronique, écouvillons pour salle blanche are indispensable tools that ensure the quality and reliability of electronic components and devices. Given the delicate nature of this industry, precision and care are paramount when handling sensitive components. This article delves into the crucial factors to consider when selecting the best cleanroom swabs for electronics manufacturing, highlighting the significance of product quality, cleanliness, and compatibility.
Understanding the Electronics Manufacturing Environment
Electronics manufacturing is conducted in controlled environments known as cleanrooms. These specialized spaces are designed to minimize particle contamination, static electricity, and other potential hazards to electronic components. The stringent cleanliness standards of cleanrooms are vital because even the smallest particle or impurity can cause product defects and failures.
Importance of Cleanroom Swabs
Cleanroom swabs play a pivotal role in the assembly and maintenance of electronic components within these pristine environments. They are used for various critical tasks, y compris:
- Cleaning Surfaces: Swabs effectively remove dust, résidus, and contaminants that can adversely affect the manufacturing process or product quality.
- Applying Solvents: They allow for the precise application of cleaning solutions, adhésifs, and other chemicals essential during manufacturing.
- Sampling: Swabs are used for sampling and quality control to ensure that both the environment and components meet stringent cleanliness standards.
Key Factors to Consider When Choosing Cleanroom Swabs
Selecting the right cleanroom swabs is crucial for maintaining the integrity of electronic components. Here are the key factors to consider:
Material Composition
The material of the swab tip is critical. It should be:
- Lint-Free: To prevent shedding tiny fibers that could contaminate components.
- Non-Abrasive: To avoid scratching or damaging delicate surfaces.
- Particle-Free: Common materials include foam, polyester, and microfiber, chosen for their minimal particle generation.
Size and Shape
The size and shape of the swab should be suited to the specific task:
- Small Swabs: Ideal for precision cleaning and sampling.
- Large Swabs: Better for covering extensive surfaces quickly.
Tip Configuration
Swab tips come in various configurations, such as:
- Pointed: For precision cleaning in tight spaces.
- Rounded: For general-purpose cleaning.
- Chiseled: For scraping off residues or applying solutions more effectively.
Compatibilité
Ensure that the swabs are compatible with the solvents and chemicals used in your manufacturing process. Some materials may degrade or react negatively with certain substances, compromising their effectiveness.
Faible génération de particules
Swabs should be designed to minimize particle generation, which is crucial in cleanroom environments where even the tiniest particles can lead to defects.
ESD (Décharge électrostatique) Control
Swabs with antistatic properties are essential to prevent electrostatic discharge, which can damage sensitive electronic components.
Emballage
The packaging of the swabs should be clean, sealed, and able to maintain their cleanliness until use. Proper packaging ensures that the swabs remain uncontaminated and ready for immediate application.