Cleanroom swabs are essential tools for cleaning surfaces in a controlled environment, such as a cleanroom. Cleanroom swabs are different from ordinary cotton swabs because they are cleaned in a cleanroom and packaged into bags after purification treatment. They are specially formulated to reduce the potential for lint and other residue, among other specialized features.
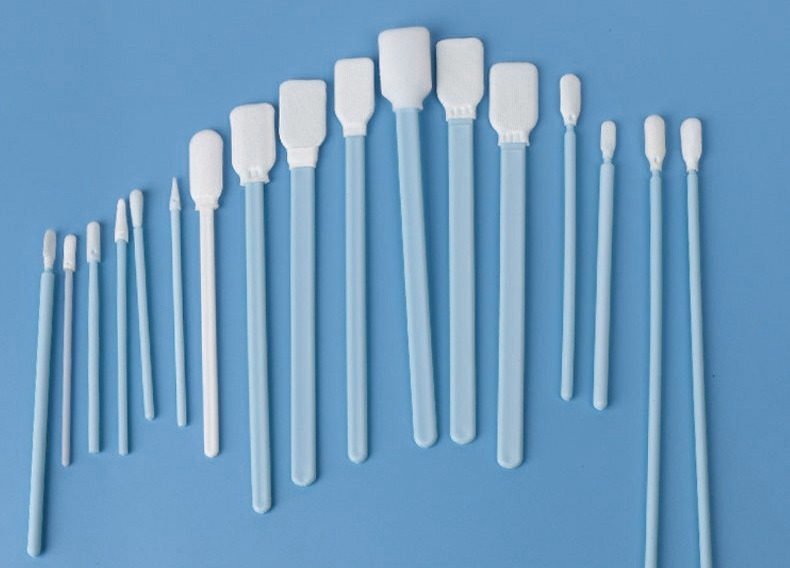
When choosing a cleanroom swab, there are a few product attributes to consider. One important and common focus in every cleanroom is to limit airborne particulate. The proper swab should be chosen to ensure the environment is not compromised. The following are some factors to consider when selecting a cleanroom swab:
- Absorption capacity: The swab should be able to absorb the cleaning agent or liquid contaminants that it will be used on.
- Linting: The swab should not leave any residue or fibers that could contaminate the surface being cleaned.
- Abrasiveness: The swab should not scratch or damage the surface being cleaned.
- Chemical resistance: The swab should be able to withstand the chemical agents it will be used with.
- Décharge électrostatique (ESD) properties: The swab should not generate static electricity that could damage sensitive equipment.
Cleanroom swab handles can be made of different materials, including wood, polypropylene, and paper. Each material has its own benefits and applications. Paper is stiff, nettoyer, and makes for a “green” tip-to-toe construction. Cependant, it contains particulates, so it is not typically recommended for cleanrooms.
Cleanroom swab tips come in varying shapes, including pointed, rectangular, and corkscrew, to aid users in specific cleaning or application tasks. The option selected will depend upon the need for absorption of cleaning agents or liquid contaminants, allowable abrasiveness and potential for linting, and other features. Foam swabs are known for their high absorbency and low-linting properties. Cotton swabs are good for general cleaning, while microfiber swabs are ideal for cleaning small parts or difficult-to-reach areas.
Cleanroom swab manufacturers are continually identifying and evaluating new swab fabrics and materials, as well as working to improve the efficiency, quality, and cleanliness of their production processes. The major swab and wipe suppliers do not themselves manufacture materials, which means they must rely largely on the development efforts of textile and foam suppliers. Given the relatively small size of the market, cleanroom applications do not get the lion`s share of research attention from these companies. Instead, wipe manufacturers largely meet critical cleanroom requirements through value-added processing of conventional materials in controlled environments, principally, proprietary laundering processes.
En conclusion, when using cleanroom swabs, it is essential to choose swabs that meet the specific needs of the application. Cleanroom swabs are specially formulated to reduce the potential for lint and other residue, among other specialized features. When choosing a cleanroom swab, the swab tip and shaft material should be considered, as well as the absorption capacity, linting, abrasiveness, chemical resistance, and ESD properties. Foam swabs are known for their high absorbency and low-linting properties, while cotton swabs are good for general cleaning. Cleanroom swab manufacturers are continually identifying and evaluating new swab fabrics and materials, as well as working to improve the efficiency, quality, and cleanliness of their production processes.