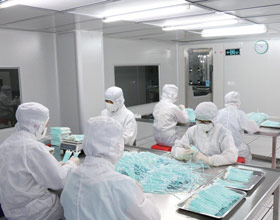
Cleanroom swabs may seem like a small and insignificant tool, but they play a crucial role in ensuring high-quality manufacturing processes. These specialized swabs are designed to meet the stringent requirements of cleanroom environments, where even the tiniest contamination can have severe consequences.
Cleanrooms are controlled environments used in industries such as pharmaceuticals, electronics, and biotechnology. They are designed to minimize airborne particles, damm, and other contaminants that could compromise the production process. Maintaining cleanliness is essential to prevent product defects, equipment failures, and costly reworks.
One of the primary sources of contamination in cleanrooms is human contact. Our bodies naturally shed dead skin cells, hair, and oils, which can contain microbes or particles. When these particles enter the manufacturing process, they can lead to product failures or affect the performance of sensitive equipment.
This is where cleanroom swabs come into play. They are specially designed to effectively remove contaminants from delicate surfaces without leaving any residue behind. The materials used in these swabs are carefully selected to ensure they do not introduce additional contaminants into the cleanroom environment.
Cleanroom swabs are available in various materials, such as polyester, foam, eller mikrofiber. Each material has unique properties that make it suitable for different cleaning tasks. Till exempel, foam swabs are excellent for absorbing liquids, while polyester swabs are ideal for removing particles from surfaces.
The design of cleanroom swabs also contributes to their effectiveness. They are typically manufactured with a low-linting or non-linting construction to prevent fiber shedding. Moreover, the swabs are engineered to have a consistent shape and size, ensuring uniform cleaning and reducing the risk of leaving behind any residue.
In addition to their cleaning capabilities, cleanroom swabs also help with quality control. Regular swabbing of critical surfaces allows manufacturers to monitor cleanliness levels and identify potential sources of contamination. By identifying and addressing these issues promptly, manufacturers can prevent costly production delays or product recalls.
It is important for companies operating in cleanroom environments to establish proper protocols for swabbing procedures. This includes selecting the appropriate swab material, following recommended techniques for surface cleaning, and disposing of used swabs properly.
Sammanfattningsvis, cleanroom swabs are essential tools that contribute to high-quality manufacturing processes. By effectively removing contaminants from critical surfaces, they help prevent product defects, equipment failures, and costly reworks. Proper utilization of cleanroom swabs, along with stringent cleanliness protocols, ensures that manufacturing processes meet the highest standards of quality and reliability.