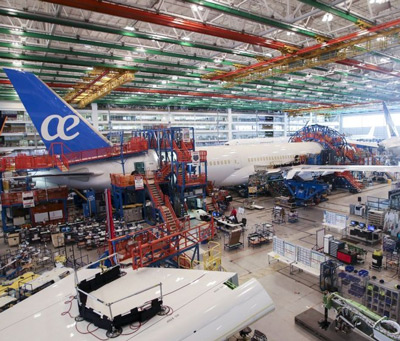
The aerospace industry is highly demanding, with a crucial need for precision, accuracy, and reliability. Any form of contamination, no matter how small, can have severe consequences on the performance and safety of aerospace equipment. To combat this issue, the industry relies heavily on cleanroom environments and specialized cleaning tools, such as renrumspinnar. I den här artikeln, we will explore the importance of cleanroom swabs in preventing contamination in the aerospace industry and how they contribute to maintaining the highest standards of quality control.
1. The importance of contamination prevention in the aerospace industry
Contamination in the aerospace industry can arise from various sources, including particulates, chemicals, rester, and even human skin flakes. These contaminants can disrupt the functioning of equipment, degrade materials, and compromise the performance of critical components. Moreover, contamination control is vital to ensure the safety of astronauts, passengers, and crew members who rely on aerospace technology.
2. Understanding cleanroom environments
Cleanrooms are controlled environments designed to minimize airborne contaminants and maintain specific cleanliness levels. Different classes of cleanrooms adhere to international standards, ensuring the highest levels of cleanliness and minimizing the risk of contamination. The aerospace industry often requires cleanrooms with stringent cleanliness standards, such as ISO Class 5 or better.
3. Role of cleanroom swabs in contamination prevention
Cleanroom swabs play a crucial role in contamination prevention within the aerospace industry. These specialized tools are designed to effectively clean sensitive equipment and surfaces without leaving behind residues or fibers. Cleanroom swabs are made from low-linting materials, such as polyester, foam, eller mikrofiber, which reduce the chances of particle generation during the cleaning process.
4. Types of cleanroom swabs
There are various types of cleanroom swabs available, each designed for specific cleaning requirements. Foam swabs are commonly used for general purpose cleaning, while polyester swabs are suitable for critical cleaning tasks. Microfiber swabs are ideal for cleaning delicate optics and precision instruments, as they offer superior cleaning efficiency and low abrasion.
5. Proper handling and usage of cleanroom swabs
To maximize the effectiveness of cleanroom swabs, proper handling and usage are essential. Users must follow strict protocols, including wearing cleanroom garments, handskar, and using approved cleaning solutions. Swabs should be used with minimal pressure and in a controlled manner to avoid damage to surfaces or equipment.
6. Regular swab testing and quality control
To ensure the reliability and effectiveness of cleanroom swabs, regular testing and quality control measures must be implemented. This includes monitoring swabs for particulate contamination, chemical residues, and overall cleanliness. Swab manufacturers often provide certifications and documentation to validate their products’ suitability for cleanroom use.
Slutsats:
Contamination prevention is of utmost importance in the aerospace industry, where precision, pålitlighet, and safety are paramount. Cleanroom swabs play a significant role in maintaining the required cleanliness standards and ensuring the flawless operation of aerospace equipment. By using the right cleanroom swabs and following proper handling procedures, the industry can minimize the risk of contamination and uphold the highest standards of quality control.