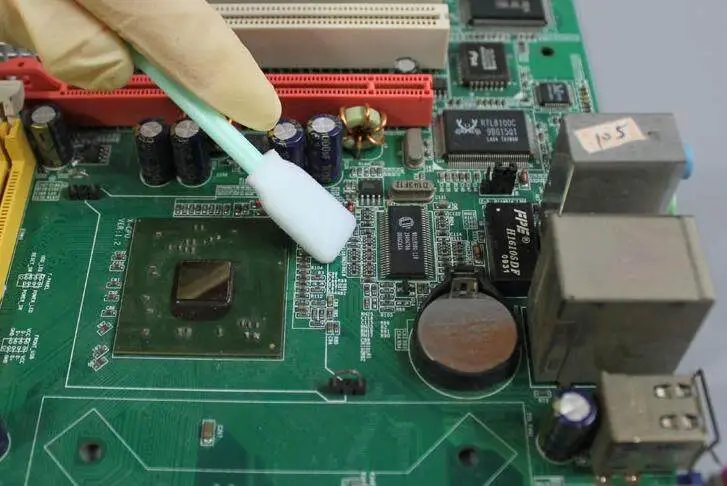
PCB flux removal can either happen at the benchtop, which generally requires a manual cleaning method. This is common for low volume electronic PCB assembly, rework, and repair. Manual cleaning methods are generally more laborious and less repeatable, so results may vary from operator to operator. For higher volume assembly or reduced variability, more automated cleaning methods are used.
Manual Flux Removal Methods
- Aerosol– Aerosol flux removers have the advantage of a sealed system, which ensures fresh solvent every time, and agitation provided by the spray pressure and pattern. A straw attachment is generally included to spray into areas with greater precision.
- Aerosol w/brush attachment– A brush can be added to the aerosol nozzle, so the solvent sprays through the brush as you scrub.
- Trigger spray– Trigger spray bottles are more common for water-based cleaners and isopropyl alcohol (異丙醇), but not for aggressive solvent cleaners.
- Liquid immersion– The PCB can be immersed into a tray or bucket of solvent cleaner, with cleaning tools like swabs and brushes used as needed for tenacious soils. Cleaning performance can be further improved by heating the solvent, but this should only be done with nonflammable flux removers.
- Spot cleaning with a cleanroom swab– A cotton or foam swab can be saturated with a mild solvent like isopropyl alcohol, often from a pump dispenser or “dauber”.
- Presaturated wipes and swabs– For added convenience, wipes and swabs are available presaturated with a mild solvent like isopropyl alcohol.
Automated or Semi-Automated Flux Removal Methods - Ultrasonic– Ultrasonic cleaning equipment use sound waves to create implosions within the flux residue, breaking it apart and lifting it off the PCB. Most equipment have the option of heating the solvent to increase cleaning performance. Only use this option with a nonflammable flux remover. Cross contamination can be a concern, so change solvent regularly. Ultrasonic cleaning might be too rough on sensitive components like ceramic-based resisters.
- Vapor degreaser– Vapor degreasing is the go-to process for the highest precision cleaning, like used for aerospace and medical electronics. PCBs can be submerged in a sump of boiling solvent, in a rinse sump with ultrasonics, and rinsed in solvent vapors. Special solvents need to be used that are azeotropes or near-azeotropes, so will not change as the solvents are boiled off and reconstituted in a continuous cycle.
- Batch flux remover– Basically a dishwasher for electronic circuit boards. PCBs are stationary in a rack, and the flux remover (usually water-based) is sprayed over the assembly. The PCB stays in place as the machine goes through the wash, rinse and finally dry cycle.
- Inline flux remover– An inline washer is more like a carwash for electronic circuit boards. PCBs travel on a conveyor through wash, rinse and dry zones. Water-based flux removers are used.
This article reprinted in Chemtronics